COURSE OVERVIEW
PE0912 : Advanced Refinery Operations, Plants Process & Troubleshooting
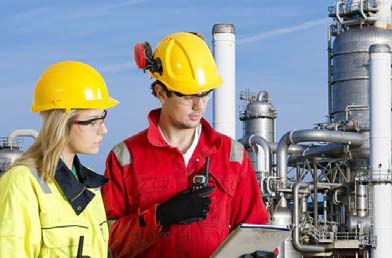
OVERVIEW
COURSE TITLE | : | PE0912 : Advanced Refinery Operations, Plants Process & Troubleshooting |
COURSE DATE | : | Aug 17 - Aug 21 2025 |
DURATION | : | 5 Days |
INSTRUCTOR | : | Dr. John Petrus |
VENUE | : | Istanbul, Turkey |
COURSE FEE | : | $ 6000 |
Request For Course Outline |
Course Description
This practical and highly-interactive course includes reallife
case studies and exercises where participants will be
engaged in a series of interactive small groups and class
workshops.
Refinery processes consist of many complex apparatuses
involving both moving and static parts as well as
interconnecting pipes, control mechanisms and electronics,
mechanical and thermal stages, heat exchangers, waste and
side product processing units, power ducts and many others.
Bringing such a complicated unit online and ensuring its
continued productivity requires substantial skill at anticipating,
detecting and solving acute problems. Failure to identify and
resolve these problems quickly can lead to lost production,
off-spec product, equipment loss, and even catastrophic
accidents. Therefore, the ability to troubleshoot refinery
operations is one of the most valuable skills operations
personnel can possess.
Typical refineries operate about 26 days of the month to cover
costs. The remaining days in the month they operate to make
a profit. If the process is down for five days, then the company
cannot cover costs and no profit has been made. Engineers
must quickly and successfully solve any troublesome
problems that occur. Sometimes the problems occur during
startup; sometimes, just after a maintenance turn-around; and
sometimes unexpectedly during usual operation. A
troubleshooting problem is one where something occurs that
is unexpected to such an extent that it is perceived that some
corrective action may be needed. The trouble usually occurs
somewhere in a system that consists of various pieces of
interacting equipment run by people.
Troubleshooting is the process used to diagnose the fault safely and efficiently, decide
on corrective action and prevent the fault from reoccurring. Process engineering,
especially troubleshooting, is different from most other branches of technology in
another respect: It is not advancing very quickly. The principles of distillation,
hydraulics, phase separation, and heat transfer, as they apply to process applications,
have been well known for quite some time. The challenge in troubleshooting consists of
untangling the influence that human error, mechanical failure, and corrosion have on
these well-known principles. The aspect of the job that makes it so difficult is that most
refinery problems are initiated by human error – a never-ending source of surprise.
Most Refinery troubles have a simple origin. However, this simple origin is clouded by
false data, misconceptions, superficial observations, and third-hand reports. The error
that most engineers often make is that they develop a theory, usually with process
computer simulations, as to the cause of the malfunction. The theory is then reviewed
with management and other technical personnel at a large meeting. If no one objects to
the theory, it is accepted as the solution to the problem. Technical training is one tool
that should be taken into the field to reveal the underlying problem, but confining the
investigation to technical areas only will severely limit the chances of success.
link to course overview PDF
case studies and exercises where participants will be
engaged in a series of interactive small groups and class
workshops.
Refinery processes consist of many complex apparatuses
involving both moving and static parts as well as
interconnecting pipes, control mechanisms and electronics,
mechanical and thermal stages, heat exchangers, waste and
side product processing units, power ducts and many others.
Bringing such a complicated unit online and ensuring its
continued productivity requires substantial skill at anticipating,
detecting and solving acute problems. Failure to identify and
resolve these problems quickly can lead to lost production,
off-spec product, equipment loss, and even catastrophic
accidents. Therefore, the ability to troubleshoot refinery
operations is one of the most valuable skills operations
personnel can possess.
Typical refineries operate about 26 days of the month to cover
costs. The remaining days in the month they operate to make
a profit. If the process is down for five days, then the company
cannot cover costs and no profit has been made. Engineers
must quickly and successfully solve any troublesome
problems that occur. Sometimes the problems occur during
startup; sometimes, just after a maintenance turn-around; and
sometimes unexpectedly during usual operation. A
troubleshooting problem is one where something occurs that
is unexpected to such an extent that it is perceived that some
corrective action may be needed. The trouble usually occurs
somewhere in a system that consists of various pieces of
interacting equipment run by people.
Troubleshooting is the process used to diagnose the fault safely and efficiently, decide
on corrective action and prevent the fault from reoccurring. Process engineering,
especially troubleshooting, is different from most other branches of technology in
another respect: It is not advancing very quickly. The principles of distillation,
hydraulics, phase separation, and heat transfer, as they apply to process applications,
have been well known for quite some time. The challenge in troubleshooting consists of
untangling the influence that human error, mechanical failure, and corrosion have on
these well-known principles. The aspect of the job that makes it so difficult is that most
refinery problems are initiated by human error – a never-ending source of surprise.
Most Refinery troubles have a simple origin. However, this simple origin is clouded by
false data, misconceptions, superficial observations, and third-hand reports. The error
that most engineers often make is that they develop a theory, usually with process
computer simulations, as to the cause of the malfunction. The theory is then reviewed
with management and other technical personnel at a large meeting. If no one objects to
the theory, it is accepted as the solution to the problem. Technical training is one tool
that should be taken into the field to reveal the underlying problem, but confining the
investigation to technical areas only will severely limit the chances of success.
TRAINING METHODOLOGY
This interactive training course includes the following training methodologies:
LecturesPractical Workshops & Work Presentations
Hands-on Practical Exercises & Case Studies
Simulators (Hardware & Software) & Videos
In an unlikely event, the course instructor may modify the above training methodology for technical reasons.
VIRTUAL TRAINING (IF APPLICABLE)
If this course is delivered online as a Virtual Training, the following limitations will be applicable:
Certificates | : | Only soft copy certificates will be issued |
Training Materials | : | Only soft copy materials will be issued |
Training Methodology | : | 80% theory, 20% practical |
Training Program | : | 4 hours per day, from 09:30 to 13:30 |
RELATED COURSES
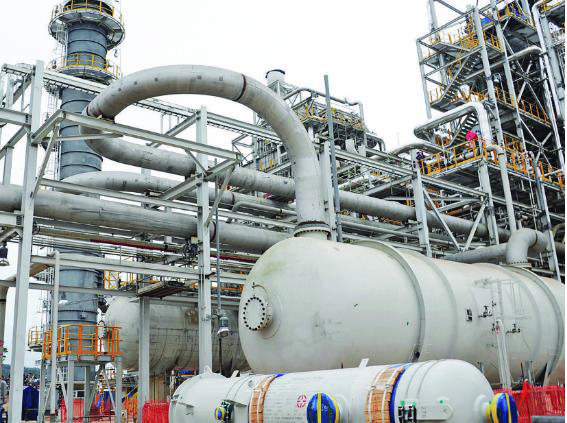
PE0630 : Urea Manufacturing Process Technology
- Date: Aug 24 - Aug 28 / 3 Days
- Location: Dubai, UAE
- Course Details Register
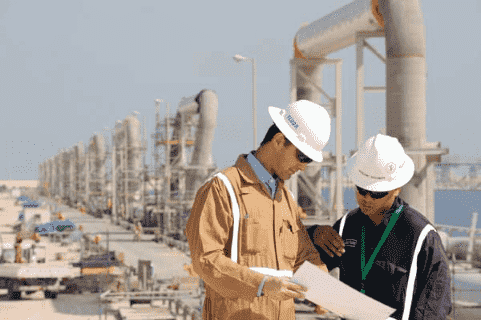
PE0248 : Process Plant Shutdown, Turnaround, Troubleshooting, Critical Activities, Isolation, Start-up & Commissioning
- Date: Aug 24 - Aug 28 / 3 Days
- Location: Kuwait City, Kuwait
- Course Details Register
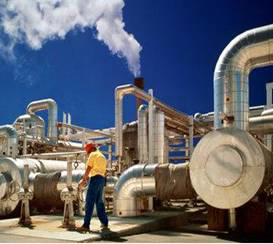
PE0230 : Process Plant Startup, Commissioning & Troubleshooting
- Date: Aug 24 - Aug 28 / 3 Days
- Location: Doha, Qatar
- Course Details Register
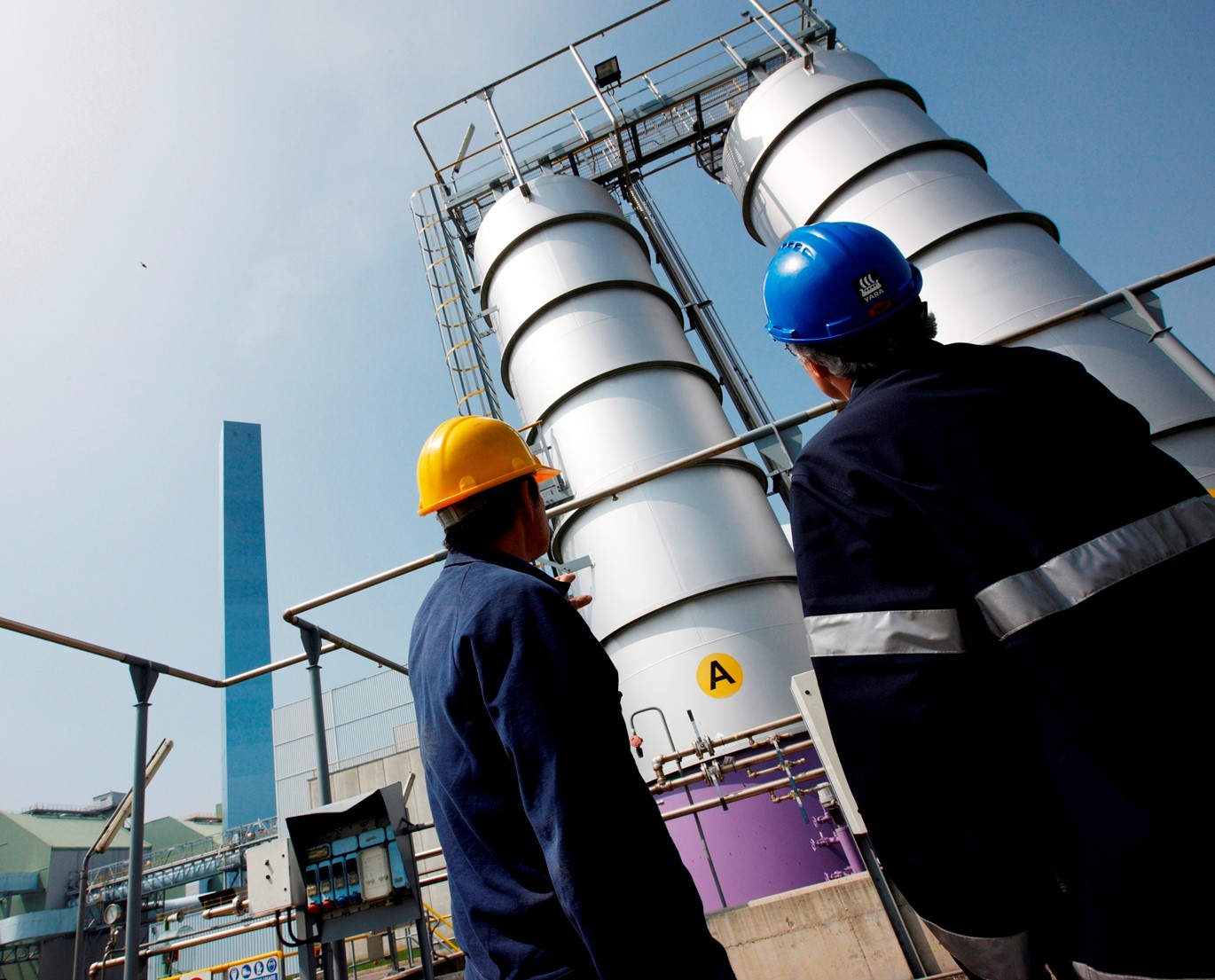
PE0061 : Advanced Fertilizers Plant Operations
- Date: Aug 24 - Aug 28 / 3 Days
- Location: Dubai, UAE
- Course Details Register