COURSE OVERVIEW
PE0105 : Process Plant Optimization, Revamping & Debottlenecking
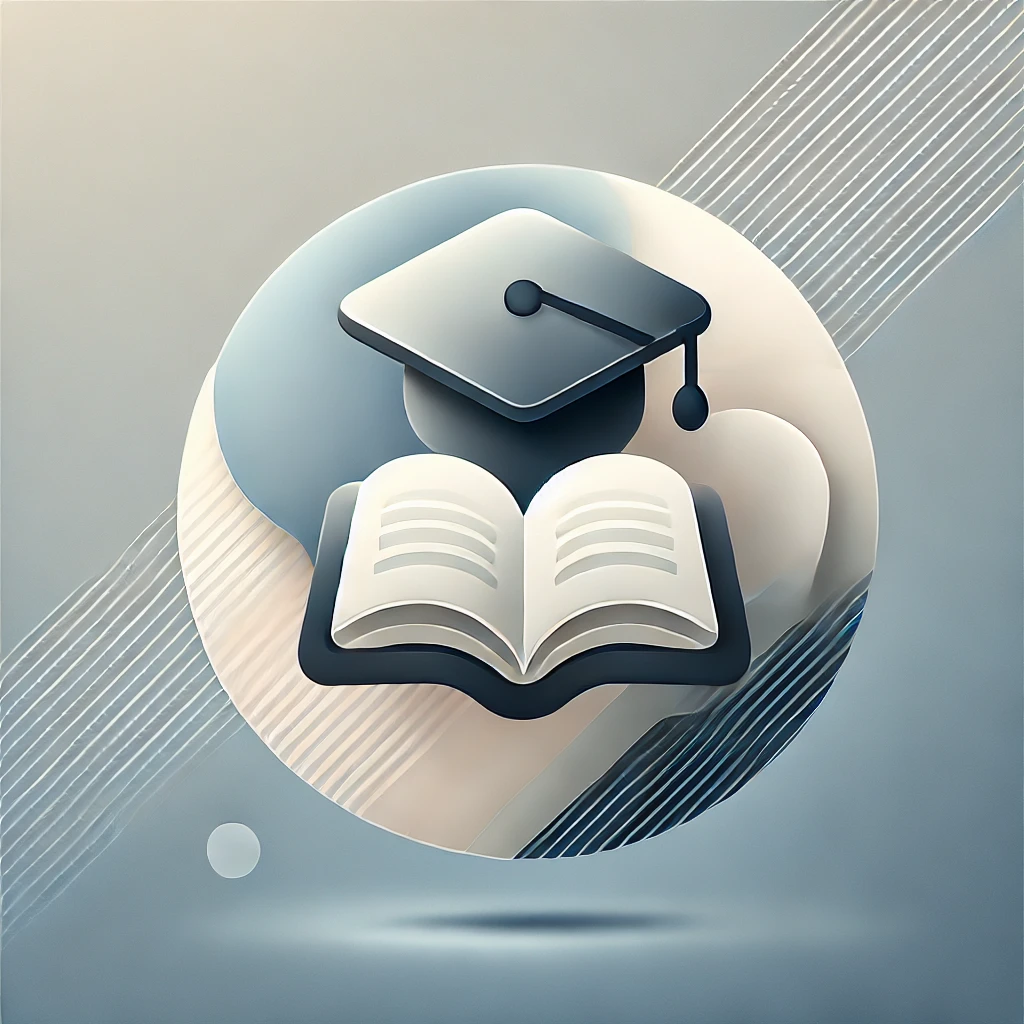
OVERVIEW
COURSE TITLE | : | PE0105 : Process Plant Optimization, Revamping & Debottlenecking |
COURSE DATE | : | Jan 05 - Jan 09 2025 |
DURATION | : | 5 Days |
INSTRUCTOR | : | Mr. Mike Poulos |
VENUE | : | Dubai, UAE |
COURSE FEE | : | $ 5500 |
Register For Course Outline |
OTHER SCHEDULED DATES
Date | : | Jan 21 - Jan 25 2024 (5 Days) | Location | : | Dubai, UAE | Classroom Fee (US$) | : | $ 5500 | Course Info |
Date | : | Feb 04 - Feb 08 2024 (5 Days) | Location | : | Dubai, UAE | Classroom Fee (US$) | : | $ 5500 | Course Info |
Date | : | Feb 05 - Feb 08 2024 (4 Days) | Location | : | Dubai, UAE | Classroom Fee (US$) | : | $ 4500 | Course Info |
Date | : | Mar 03 - Mar 07 2024 (5 Days) | Location | : | Doha, Qatar | Classroom Fee (US$) | : | $ 6000 | Course Info |
Date | : | May 06 - May 09 2024 (4 Days) | Location | : | Al Khobar, KSA | Classroom Fee (US$) | : | $ 4500 | Course Info |
Date | : | Jun 09 - Jun 13 2024 (5 Days) | Location | : | Dubai, UAE | Classroom Fee (US$) | : | $ 5500 | Course Info |
Date | : | Aug 04 - Aug 08 2024 (5 Days) | Location | : | Doha, Qatar | Classroom Fee (US$) | : | $ 6000 | Course Info |
Date | : | Aug 05 - Aug 08 2024 (4 Days) | Location | : | Doha, Qatar | Classroom Fee (US$) | : | $ 5500 | Course Info |
Date | : | Sep 15 - Sep 19 2024 (5 Days) | Location | : | Doha, Qatar | Classroom Fee (US$) | : | $ 6000 | Course Info |
Date | : | Nov 03 - Nov 07 2024 (5.0416666666667 Days) | Location | : | Dubai, UAE | Classroom Fee (US$) | : | $ 5500 | Course Info |
Date | : | Nov 11 - Nov 14 2024 (4 Days) | Location | : | Abu Dhabi, UAE | Classroom Fee (US$) | : | $ 4500 | Course Info |
Date | : | Jan 19 - Jan 23 2025 (5 Days) | Location | : | Istanbul, Turkey | Classroom Fee (US$) | : | $ 6000 | Course Info |
Date | : | May 04 - May 08 2025 (5 Days) | Location | : | Dubai, UAE | Classroom Fee (US$) | : | $ 5500 | Course Info |
Date | : | Jul 19 - Jul 23 2025 (5 Days) | Location | : | Kuwait City, Kuwait | Classroom Fee (US$) | : | $ 5500 | Course Info |
Date | : | Jul 20 - Jul 24 2025 (5 Days) | Location | : | Kuwait City, Kuwait | Classroom Fee (US$) | : | $ 5500 | Course Info |
Date | : | Jul 20 - Jul 24 2025 (5 Days) | Location | : | Kuwait City, Kuwait | Classroom Fee (US$) | : | $ 5500 | Course Info |
Date | : | Aug 03 - Aug 07 2025 (5 Days) | Location | : | Al Khobar, KSA | Classroom Fee (US$) | : | $ 5500 | Course Info |
Date | : | Nov 10 - Nov 14 2025 (5 Days) | Location | : | Abu Dhabi, UAE | Classroom Fee (US$) | : | $ 5500 | Course Info |
Course Description
This practical and highly-interactive course includes various practical sessions and exercises. Theory learnt will be applied using our state-of-the-art simulators. Process plants are normally designed to nameplate capacities stipulated at the commencement of design. However, this can be misleading. Usually plants have an inbuilt design margin that is not 'visible' to the owner, leading to false operating constraints that cost you lost revenue. On the other hand, bottlenecks are often introduced due to poor design or as a result of incomplete commissioning and poor control. These tend to result in your facility having reduced throughputs coupled with poor uptime. Not too long ago, it was generally conceded that a new plant could produce at least 10% more than its nameplate capacity. In some instances, owners would oversize certain pieces of critical equipment to assure this and possibly more. Today, however, we see plants being expanded too much higher capacities due to a combination of new technology and improved ways to operate and control them. Modernization and optimization are the key prerequisites for long-term successful plant operation. Process plants are subject to permanent adjustment pressure for optimization in the areas of new or changing feed materials, products and product specifications as well as environmental regulations and demands on energy savings. Major optimization targets are, in addition to cost cutting, plant quality and capacity improvements. Retrofitting a plant is often seen as an attractive investment option compared to a new plant. Implementing new technology ‘creeps’ the plant capabilities at minimum cost. Plant debottlenecking for incremental capacity or product quality changes costs less than a new plant. However, revamping plant is more complex than building new one. Existing equipment needs to be analyzed, performance predicted, and integrated with new equipment and process changes. Process sequence changes also require evaluation for finding the most cost effective and reliable revamp. Existing equipment poses both challenges and opportunities in a revamp. Challenges due to limitations, both hidden and obvious, must be met. Opportunities come from using underutilized capabilities of the existing equipment. Correctly identifying both limits and opportunities provides the lowest investment revamp. Processes include more than just equipment. Processes include specific linkages between equipment to achieve the operating plant objectives. Revamps must examine both the capabilities of the equipment and the opportunities available from changing the process sequence (or operating conditions). Correctly integrating equipment and process evaluation requires good field test data, an accurate analysis of the data, and putting together a proper team for a given revamp. No revamp is the same as any other. Every plant is different. All equipment and every process have different limits and different opportunities. Debottlenecking is a common term for increasing overall production capacity by identifying the limiting unit operation(s) in the process and removing this limitation. Like the weakest link in a chain, maximum production capacity of any process is limited by the lowest capacity step(s) in the process, thereby producing a "bottleneck" or narrowing of total process throughput. Identifying and eliminating "bottlenecks" is a cost-effective way to obtain a sometimes significant increase in plant overall capacity and profitability. Debottlenecking can maximize an existing plant's profitability. However, debottlenecking considerations should be taken into account during the design stage of a new facility to allow for future debottlenecking. Also, sometimes a fresh view of an operating facility can lead to debottlenecking ideas. Both revamp work and troubleshooting can be part of a plant debottlenecking effort. They share many tactics, but differ in their intent. The goal of a revamp is to improve some basic parameters such as capacity or processing efficiency. In contrast, troubleshooting merely aims to solve a problem that hampers current operation. Often, the problem exposes an opportunity for much greater gain in performance. Both revamp and troubleshooting require open-minded thinking and proficiency with engineering tools. Both often rely on test runs to diagnose problems and uncover design errors or inaccuracies in equipment ratings. However, for a major improvement in the fundamental performance of a unit, the engineer must go beyond this first level of investigation and intentionally look for the greater gain. This course is designed to provide a good overview of the process plant optimization, rehabilitation, revamping and debottlenecking. It covers process plant overview, optimization & profitability, basic and advanced optimization tools, optimizing the design, capacity creep & plant debottlenecking, cost-effective debottlenecking strategy and action plan, optimizing process operations, process controls, optimizing reliability, management & enterprise information systems, risk management & optimization, optimizing offsites operations, utilities management, rehabilitation philosophy and mechanism, revamping strategy and options, r&d role in new product development and production capacity enhancement, safety & environmental considerations, and project management issues. The course includes many case studies that will be discussed within the 5 days. However, participants are encouraged to bring their own problems and case studies to the course. These problems should be of a non-confidential nature that can be discussed without violation of any confidentiality restrictions.
link to course overview PDF
TRAINING METHODOLOGY
This interactive training course includes the following training methodologies:
LecturesWorkshops & Work Presentations
Case Studies & Practical Exercises
Videos, Software & Simulators
In an unlikely event, the course instructor may modify the above training methodology for technical reasons.
VIRTUAL TRAINING (IF APPLICABLE)
If this course is delivered online as a Virtual Training, the following limitations will be applicable:
Certificates | : | Only soft copy certificates will be issued |
Training Materials | : | Only soft copy materials will be issued |
Training Methodology | : | 80% theory, 20% practical |
Training Program | : | 4 hours per day, from 09:30 to 13:30 |
RELATED COURSES
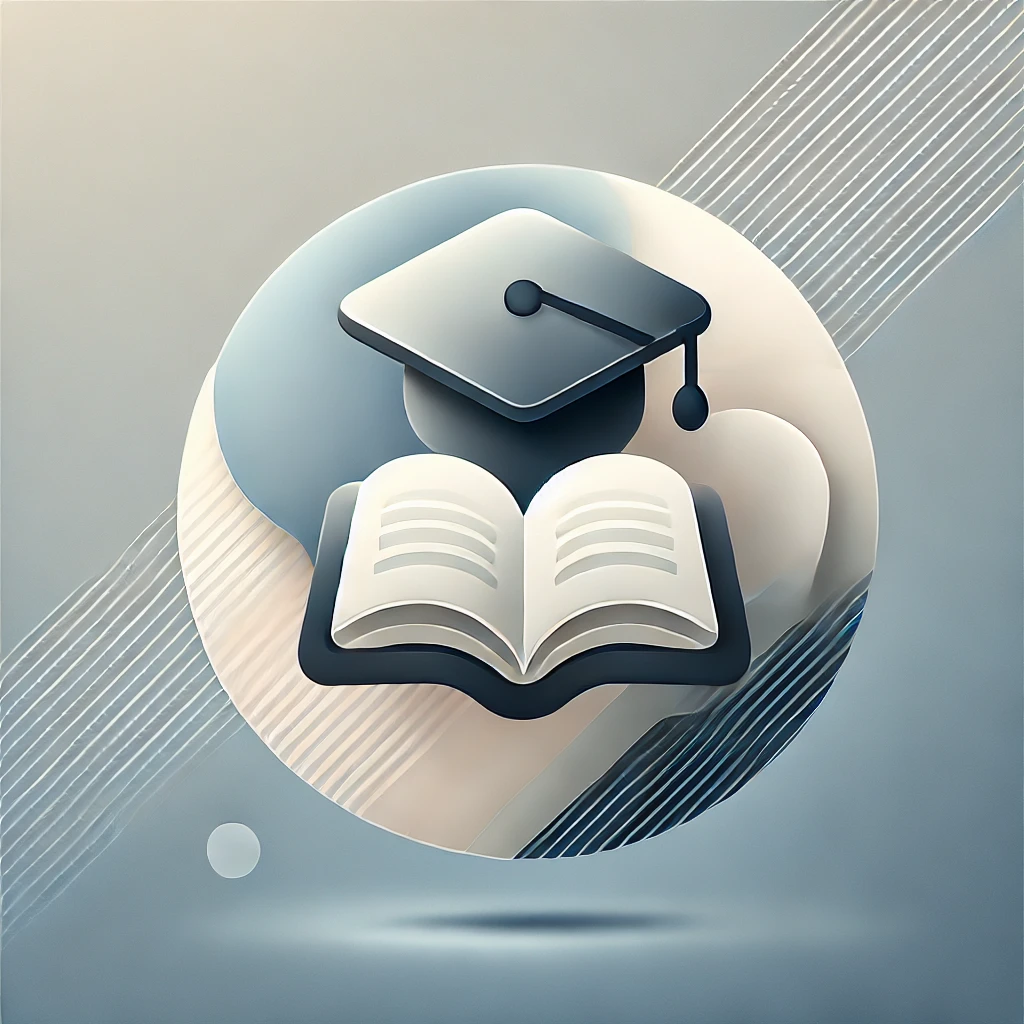
PE0105 : Process Plant Optimization, Revamping & Debottlenecking
- Date: Jan 05 - Jan 09 / 3 Days
- Location: Dubai, UAE
- Course Details Register
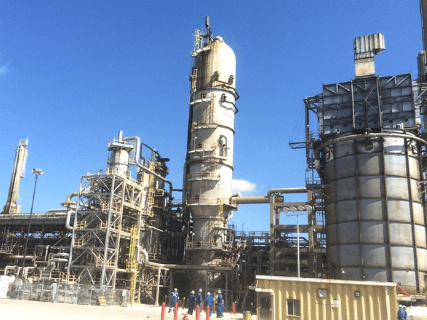
PE0390 : Distillation Design, Operation, Control & Troubleshooting
- Date: Jan 05 - Jan 09 / 3 Days
- Location: Dubai, UAE
- Course Details Register
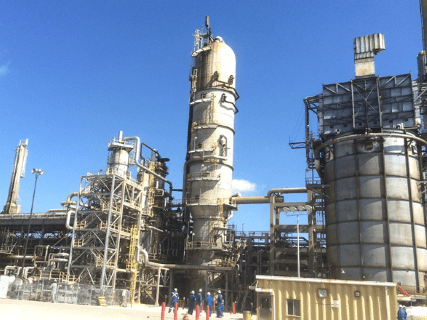
PE0390 : Distillation-Column Operation, Control & Troubleshooting
- Date: Jan 05 - Jan 09 / 3 Days
- Location: Doha, Qatar
- Course Details Register
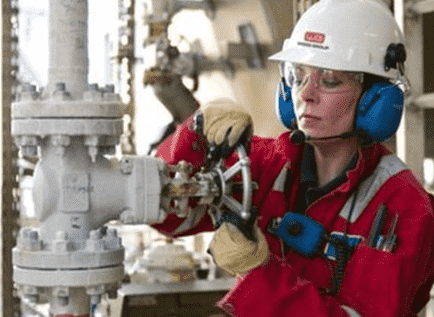
PE0102 : Certified Process Plant Operator Program
- Date: Jan 12 - Jan 16 / 3 Days
- Location: Doha, Qatar
- Course Details Register