COURSE OVERVIEW
PE0922 : Root Cause Analysis (RCA) of Upset in Process Plant
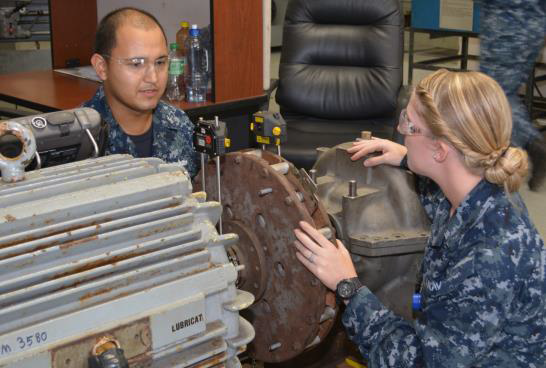
OVERVIEW
COURSE TITLE | : | PE0922 : Root Cause Analysis (RCA) of Upset in Process Plant |
COURSE DATE | : | Feb 23 - Feb 27 2025 |
DURATION | : | 5 Days |
INSTRUCTOR | : | Mr. Karl Thanasis |
VENUE | : | Dubai, UAE |
COURSE FEE | : | $ 5500 |
Register For Course Outline |
Course Description
This practical and highly-interactive course includes various practical sessions and exercises. Theory learnt will be applied using our state-of-the-art simulators.
This course is designed to provide participants with a detailed and up-to-date overview on Root Cause Analysis (RCA) of upset in process plant. It covers the operational principles and why plants get upset; finding effective solutions to event-based problems in process plant; collecting operational data like carryover, slippage, facilities, bottleneck, excess flaring, etc. and comparing with the PFDs, heart and material balance docs, data sheets and design info and PAT reports; identifying bottlenecks of facilities, instruments errors and human errors; reviewing and verifying operational reports to develop a method to solve the problems; defining the problem; and the characteristics of a troubleshooting problem and the process used to solve troubleshooting problems.
During this interactive course, participants will learn the mental problem solving process; the overall summary of major skills and a worksheet; the practical example using the troubleshooter’s worksheet; selecting valid diagnostic actions; the complex operational troubleshooting; the fundamentals of root cause analysis; using root cause analysis techniques; the cause and effect principle; the framework of RCA including why-why analysis, breakthrough, DMAIC and RCA tools; and RCA candidate selection process; using the DMAIC process; effective interviewing and finding creative solutions and effective solutions; utilizing process engineering software for identifying root cause and troubleshooting; measuring equipment/facility performance and identifying deviations from the optimum design; developing solution to the issue; the lateral learning; and facilitating a workshop.
link to course overview PDFTRAINING METHODOLOGY
This interactive training course includes the following training methodologies:
LecturesWorkshops & Work Presentations
Case Studies & Practical Exercises
Videos, Software & Simulators
In an unlikely event, the course instructor may modify the above training methodology for technical reasons.
VIRTUAL TRAINING (IF APPLICABLE)
If this course is delivered online as a Virtual Training, the following limitations will be applicable:
Certificates | : | Only soft copy certificates will be issued |
Training Materials | : | Only soft copy materials will be issued |
Training Methodology | : | 80% theory, 20% practical |
Training Program | : | 4 hours per day, from 09:30 to 13:30 |
RELATED COURSES
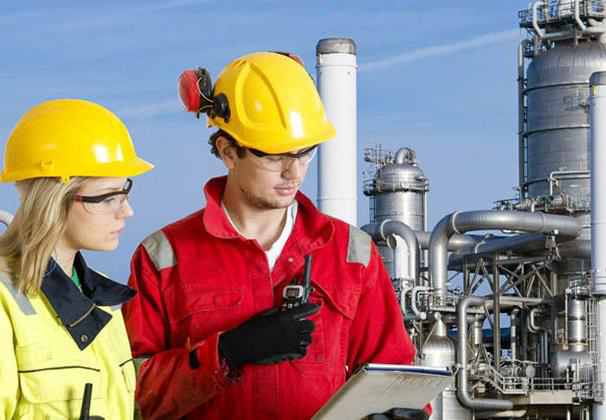
PE0902 : Refinery Process Yields Optimization
- Date: Feb 23 - Feb 27 / 3 Days
- Location: Dubai, UAE
- Course Details Register
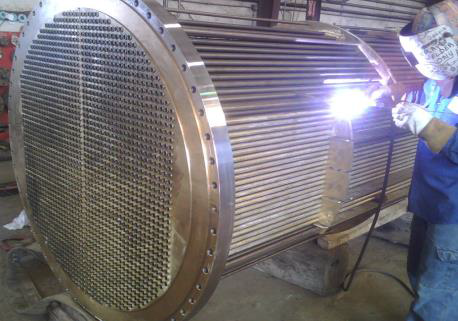
PE0382 : Heat Exchangers & Fired Heaters
- Date: Feb 23 - Feb 27 / 3 Days
- Location: London, United Kingdom
- Course Details Register
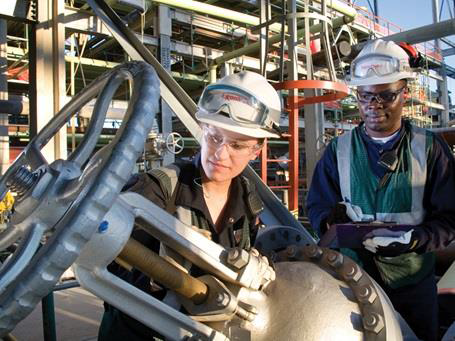
PE0120 : Catalyst Selection & Production Optimization
- Date: Feb 23 - Feb 27 / 3 Days
- Location: Al Khobar, KSA
- Course Details Register
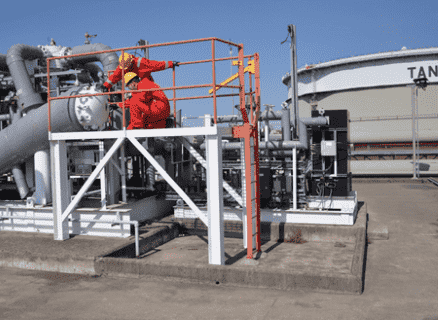
PE0010 : Oil Movement, Storage & Troubleshooting
- Date: Feb 23 - Feb 27 / 3 Days
- Location: Cairo, Egypt
- Course Details Register